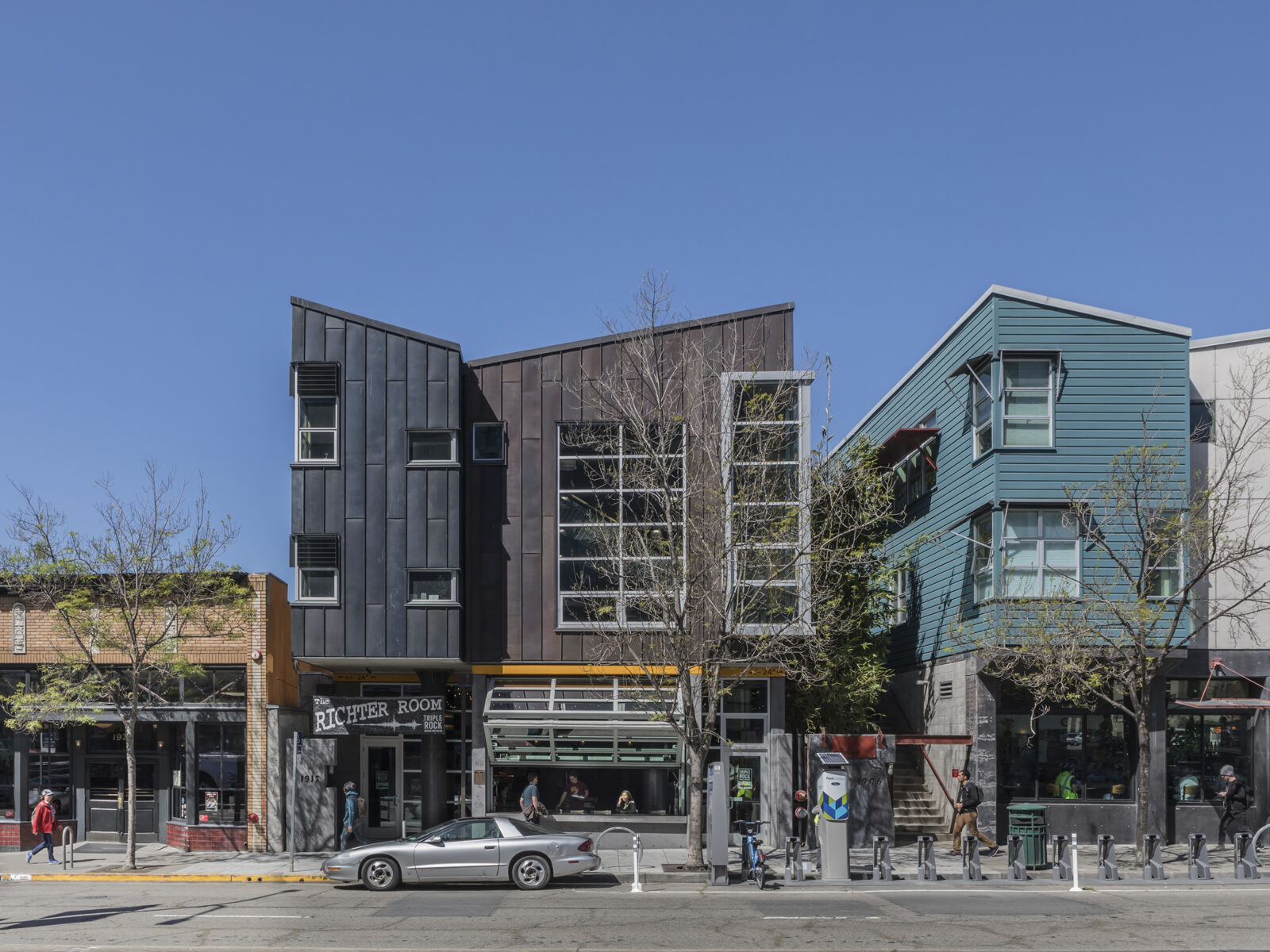
Tipping Building | 1908 Shattuck
This seismically isolated urban-infill building (and home of the Tipping Team) educates the public through radical transparency.
Seismic Resilience
This building is perhaps the country’s smallest base-isolated commercial building, with a unique seismic isolation plane: spliced into the ground-floor columns ten feet above grade, the isolator bearings are exposed and visible; ground-floor walls cantilever from the foundation, and an isolation moat is located at the second story.
Innovative Design
Splicing the building’s seismic isolation plane into the ground floor columns ten feet above grade allowed us to avoid substantial foundation work and helped fulfill our goal of educating the community about base isolation and seismic resilience.
Integrated Value
To clear zoning hurdles and maximize the size of the new building, 1906 and 1908 Shattuck were merged into one property, drastically reducing setback requirements, and allowing both buildings to share a common entry as well as the existing building’s elevator and parking garage.
The Tipping mixed-use project is the unique result of the intersection of creative engineering, real estate development, and a passion to share knowledge. Tipping—whose original Berkeley office at 1906 Shattuck is next door—developed and designed the downtown Berkeley infill project to accommodate their growing team. It includes a restaurant-brewery at street level and an office space on the second and third floors.
Challenges
The City of Berkeley is well-known for its stringent zoning codes and building requirements. A combination of these limited the size, height and number of stories of the building, and required the ground floor space to be used as retail, with office space allowed only on the upper two floors. In addition, the zoning code would have dictated a 25-foot setback on the west side of the property (which borders a residential lot), resulting in the loss of almost 2,500 square feet of usable space.
Unconventional solutions maximize usable space
Our goal for the project was to develop a structural system that reflected quintessential Tipping engineering—effective, cost-efficient, project-specific design thinking. To maximize the size of the new building, we merged 1906 and 1908 Shattuck into one property, drastically reducing setback requirements. The merger allowed both buildings to share a common entry as well as the existing building’s elevator and above-ground parking garage.
And given the seismic hazard to which the project is exposed, we wanted to design an essentially earthquake-proof building. Our design allowed us to share our knowledge about seismic resilience and base isolation with the community and resulted in perhaps the smallest isolated commercial building in the United States.
-
Location
Berkeley, CA
-
Square Footage
7,485 sf
-
Cost
$3.8 million
-
Completion Date
2016
-
Architect
Fernau and Hartman Architects
-
Contractor
Oliver and Company
-
Developer
Steven B. Tipping
-
Photography
Emily Hagopian; Tipping
AWARDS
2017 SEAONC Excellence in Structural Engineering, Award of Merit for New Construction
2017 SEAOC Excellence in Structural Engineering, Award of Excellence for New Construction
2017 NCSEA Excellence in Structural Engineering, Award of Excellence
2017 ASCE San Francisco Section Award, Outstanding Structural Engineering Project
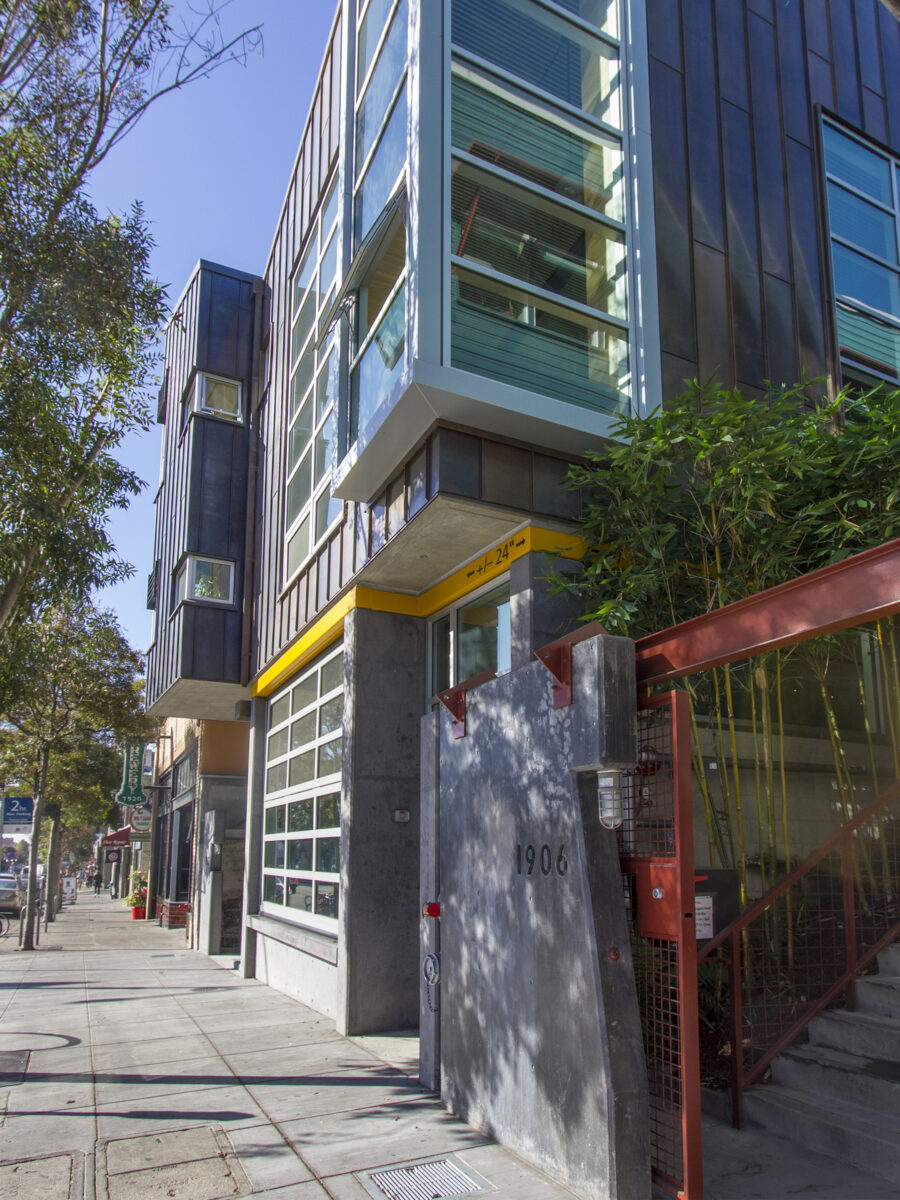
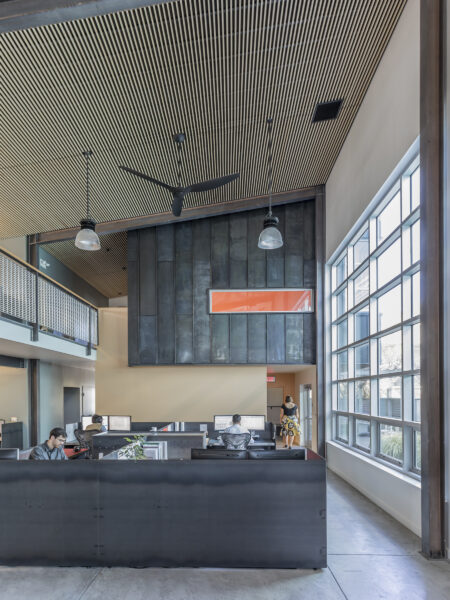
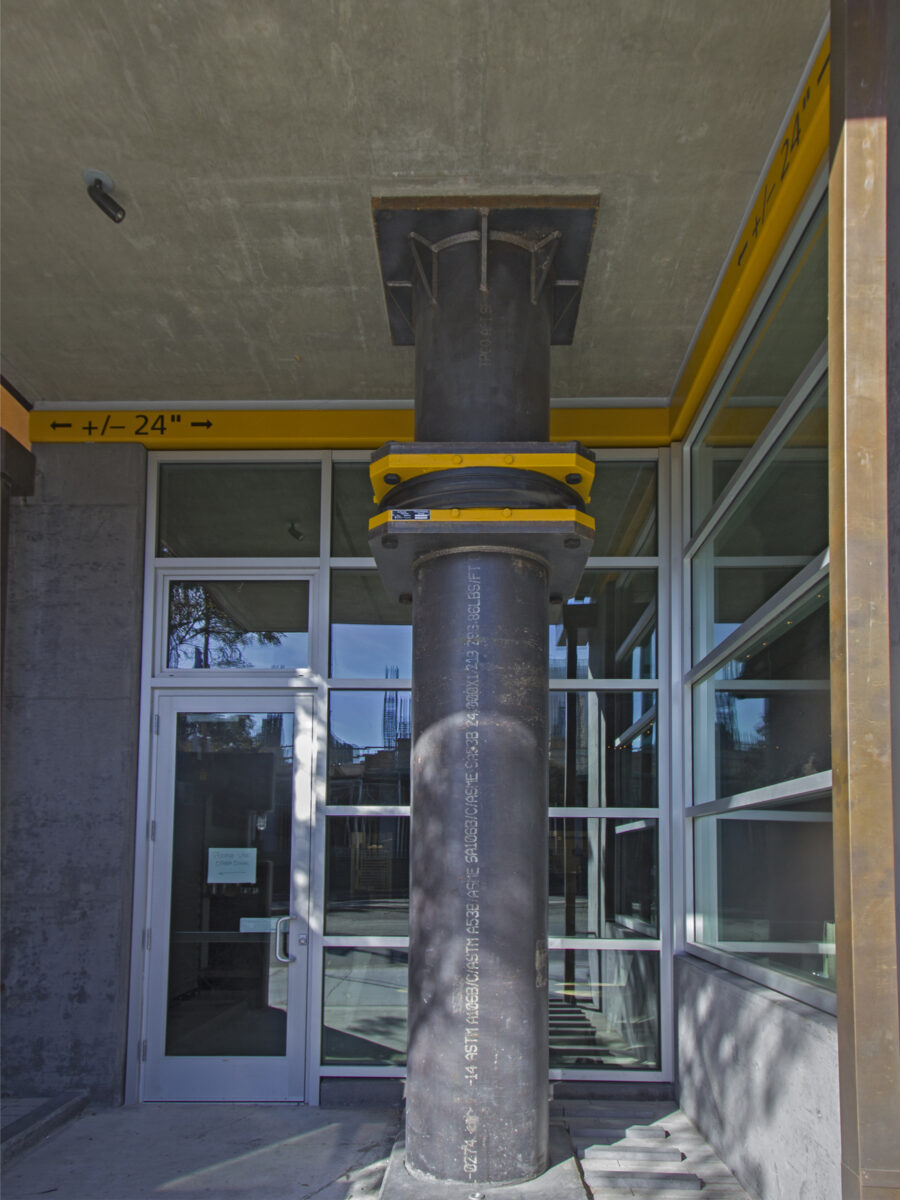
Seismic isolation on display
Once the basic geometry of the building was set and the planning and development issues resolved, we turned to designing the seismic isolation system, which became the most compelling feature of 1908 Shattuck. Isolation bearings are typically installed below grade, hidden from view, requiring intensive—and expensive—foundation work. But at our site, previous construction had left retaining walls on three sides of the lot to accommodate a grade change of about eight feet. We used this unique opportunity to create a building that would not only be at the forefront of seismic resiliency, but would educate the public about seismic isolation. Spliced into the ground-floor columns ten feet above grade, the isolator bearings are visible to restaurant patrons, while the façade design features one column viewable from the street.
While traditional base isolation systems require a ground-level moat that allows the isolated building freedom to move during an earthquake, splicing the isolation bearings into the columns above grade resulted in an atypical isolation plane that required a different solution: ground-floor walls cantilever from the foundation, and an isolation moat was designed at the second story. In the end, this unique isolation solution ended up being more cost-efficient than traditional below-grade installations.
The site’s proximity to the Hayward fault dictated isolation bearings with an allowable horizontal movement of roughly 36 inches, which would have resulted in a maximum building width of 33 feet. Tipping originally planned for a 35-foot-wide building, and given the already small lot size and the architectural program, Tipping wanted to avoid losing this additional space. We worked with Earthquake Protection Systems (EPS) in Vallejo, CA to customize six stock triple-pendulum bearings with a smaller allowable movement of 24 inches to meet seismic requirements and preserve floor space.

The seismic isolators were spliced into six steel columns ten feet above grade.
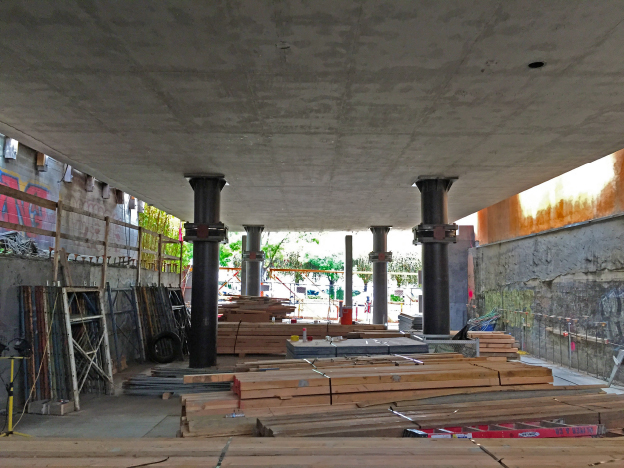
Existing walls on north and south sides of site flank isolator-spliced columns.
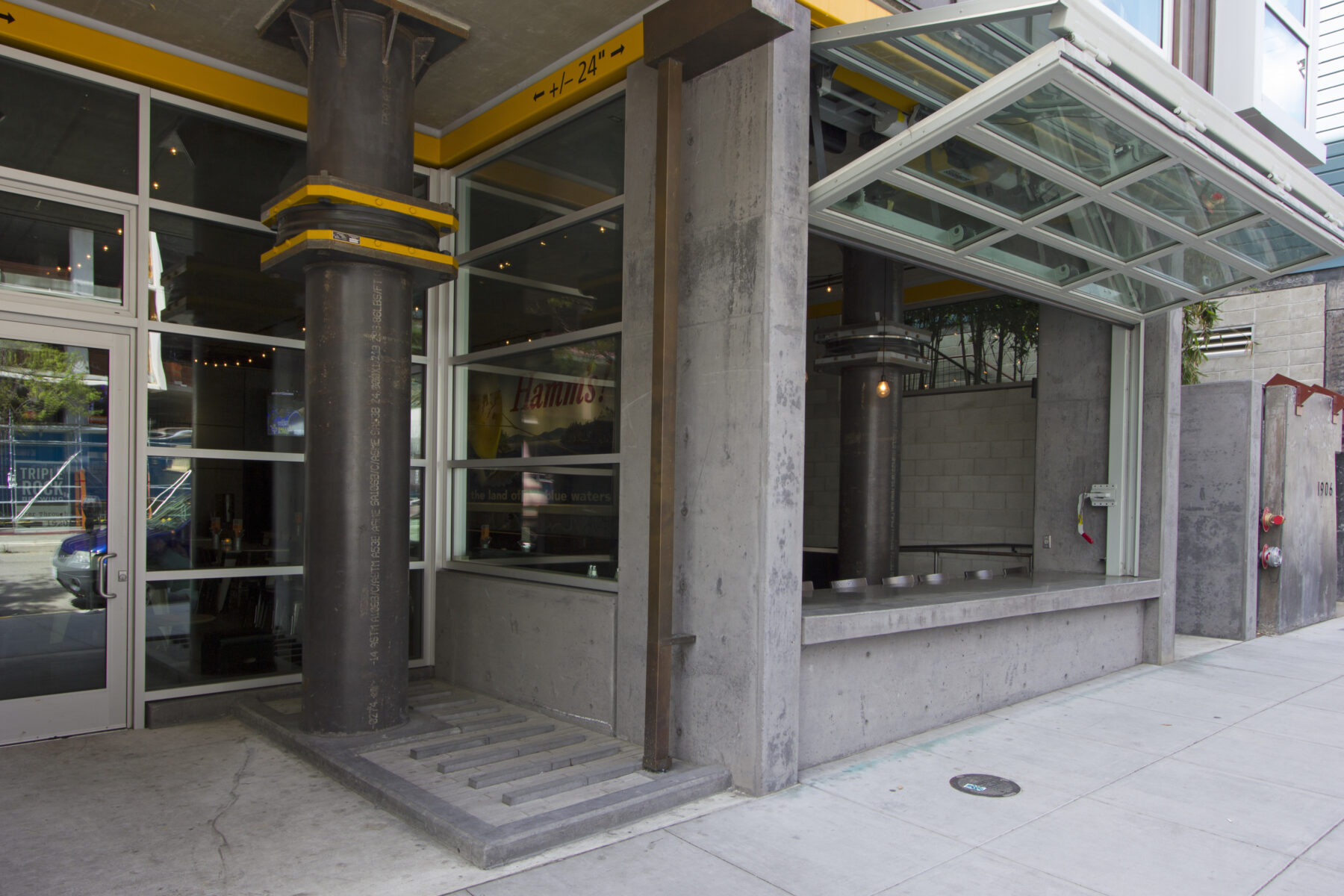
Advanced analysis + response
To ensure the custom triple pendulum bearings would meet seismic resiliency requirements, Tipping ran nonlinear response history analyses using ground motions at maximum-displacement earthquake (MCE) and design-basis earthquake (DBE) hazard levels.
Two of the 14 analyses caused the isolator to “lock up,” or reach the 24-inch allowable displacement capacity. To account for this slight probability of lock-up, we designed the cantilever columns with a larger diameter, allowing them to remain elastic at lock-up.
Then, we modeled every wood wall to analyze the effect that locking up would have on the superstructure. Based on those results, we concluded that to achieve the desired elastic behavior, all walls had to be sheathed with half-inch plywood, in some cases on both faces.
Finally, to allow the footings to yield, displace, and then self-center in the event of an earthquake force larger than the lock-up, the foundation’s grade beams were reinforced with post-tensioned high-strength steel rods. All these design moves added cost to the project, but the gain in programmable square footage was a tradeoff well worth the expense.
Exposed triple-pendulum friction bearings, highlighted in yellow for public awareness and education, allow the floors above to move 24 inches in any horizontal direction.
Statewide seismic monitoring
Tipping submitted 1908 Shattuck to the California Strong Motion Instrumentation Program for inclusion in the statewide monitoring system. It was accepted on the basis of two unique aspects: it will be the first isolated building using a wood shear-wall lateral system; and the adjacent existing office building, constructed about twenty years ago, is structurally identical to 1908, with the exception of the isolation bearings. Both buildings are hard-wired to transmit data via satellite to a data center in Sacramento, CA.
The new building is equipped with 16 three-axis sensors, the older building with six. The sensors were positioned to capture the translation and rotational components of each building’s seismic response.