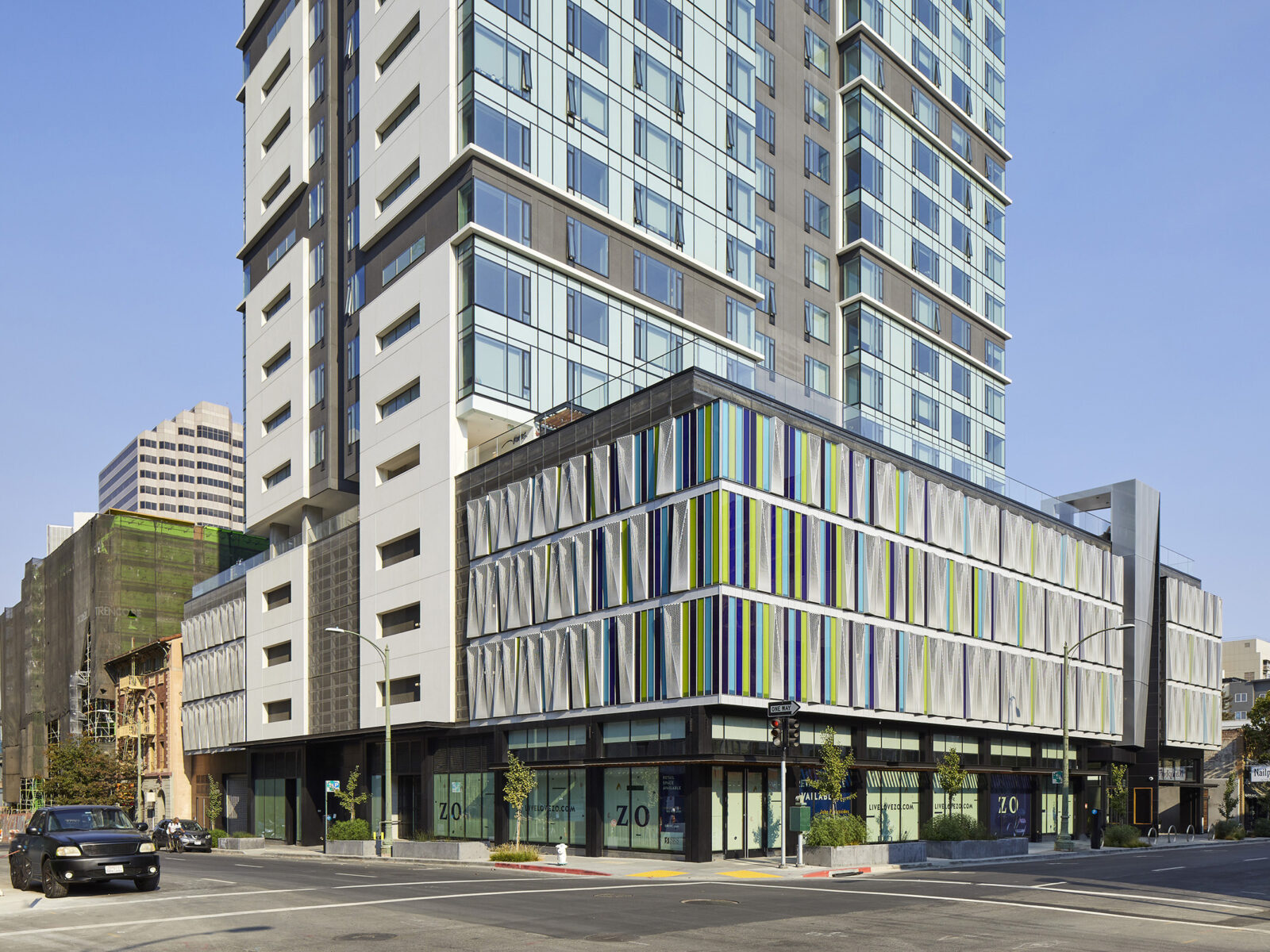
ZO Apartments
A high-rise apartment building featuring two-way post-tensioned concrete floor slabs.
Innovative Design
A simple structural solution featuring a two-way post-tensioned concrete slab system supported by concrete columns and braced with a slender concrete core provided significant cost savings for the project.
Integrated Value
The designed concrete slab system resulted in a five-day construction sequence of the tower slabs and total primary structure construction within thirteen months.
The first high-rise apartment building in downtown Oakland in a generation, 1700 Webster brings hundreds of residents, as well as new retail and restaurants, to the Lake Merritt neighborhood. Rising 23 stories above grade, the concrete-frame structure houses 204 rental units, three stories of parking, and ground floor commercial space including retail and amenity spaces for residents. A podium at the 4th level offers more communal spaces and a landscaped terrace. The rooftop, at the 23rd level, houses mechanical systems to the north and a communal pool to the south.
Challenges
Cost was a major factor in the development’s viability—while the development of housing is typically considered a safe investment in the Bay Area, the infusion of hundreds of rental units in downtown Oakland didn’t have a recent precedent to reference. The design team turned to a two-way post-tensioned concrete slab system supported by concrete columns and braced with a slender concrete core—this simple structural solution featuring thin slab profiles repeated over 23 floors would provide significant cost savings for the project. The symmetric column and core arrangement elegantly threaded the mixed-use program without disrupting the unit layouts, vehicle circulation, and commercial spaces.
Economies in a simple, efficient structural solution
Rarely in structural design can one achieve a lean, symmetrical, repeatable solution with no discontinuities. Through close collaboration with the architect and the developer, we were able to devise a symmetrical, efficient, and well integrated structural system and column grid. This system met all the needs of the mixed-use architectural program while also providing economy and improved performance.
-
Location
Oakland, CA
-
Square Footage
325,000 sf
-
Cost
$110 million
-
Completion Date
2020
-
Owner
The Green Cities Company (Formerly Gerding Edlen)
-
Architect
Perkins&Will
-
Contractor
Suffolk Construction
-
Developer
The Green Cities Company (Formerly Gerding Edlen)
-
Photography
Russell Abraham
AWARDS
LEED Gold Certified
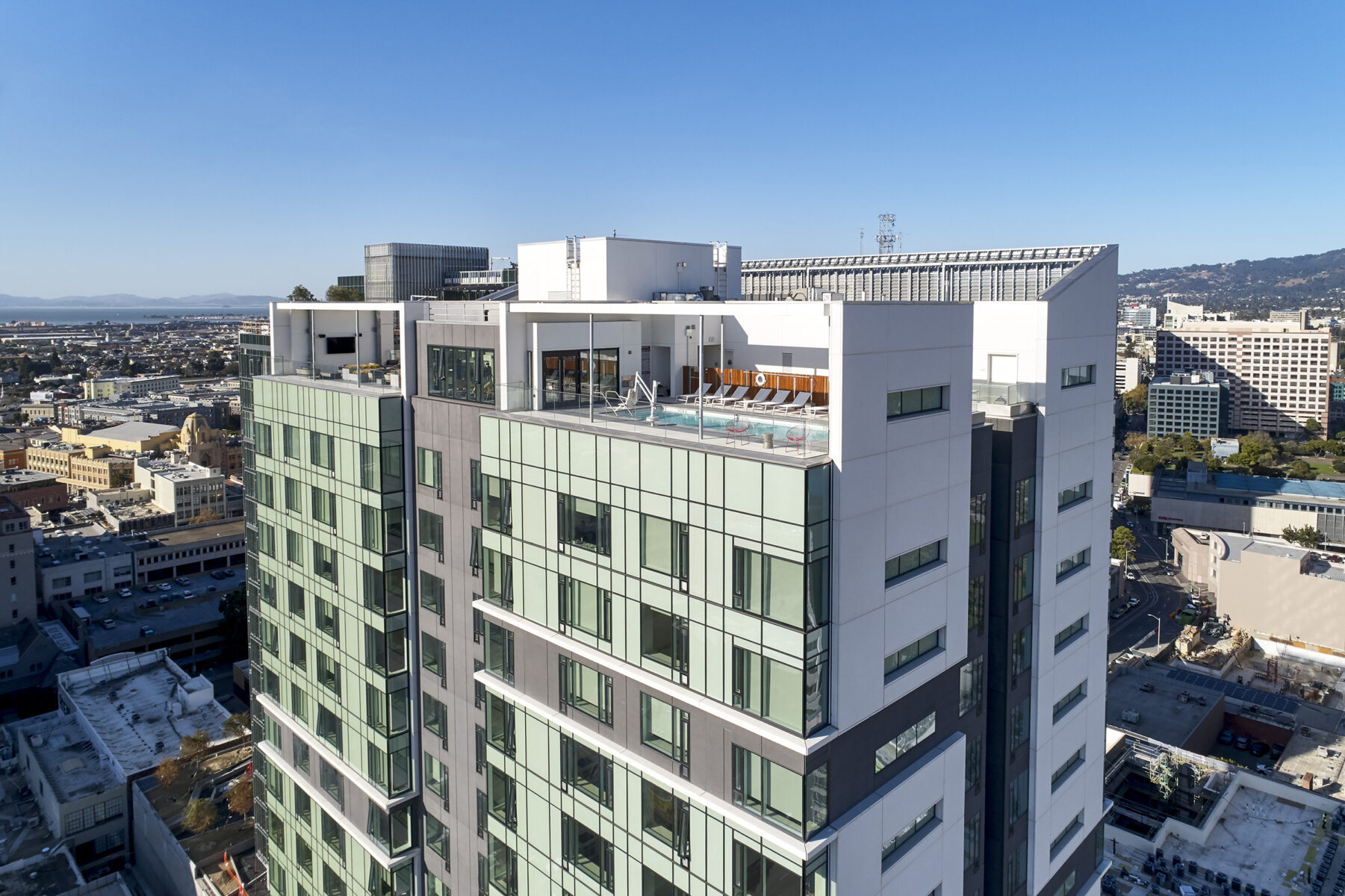
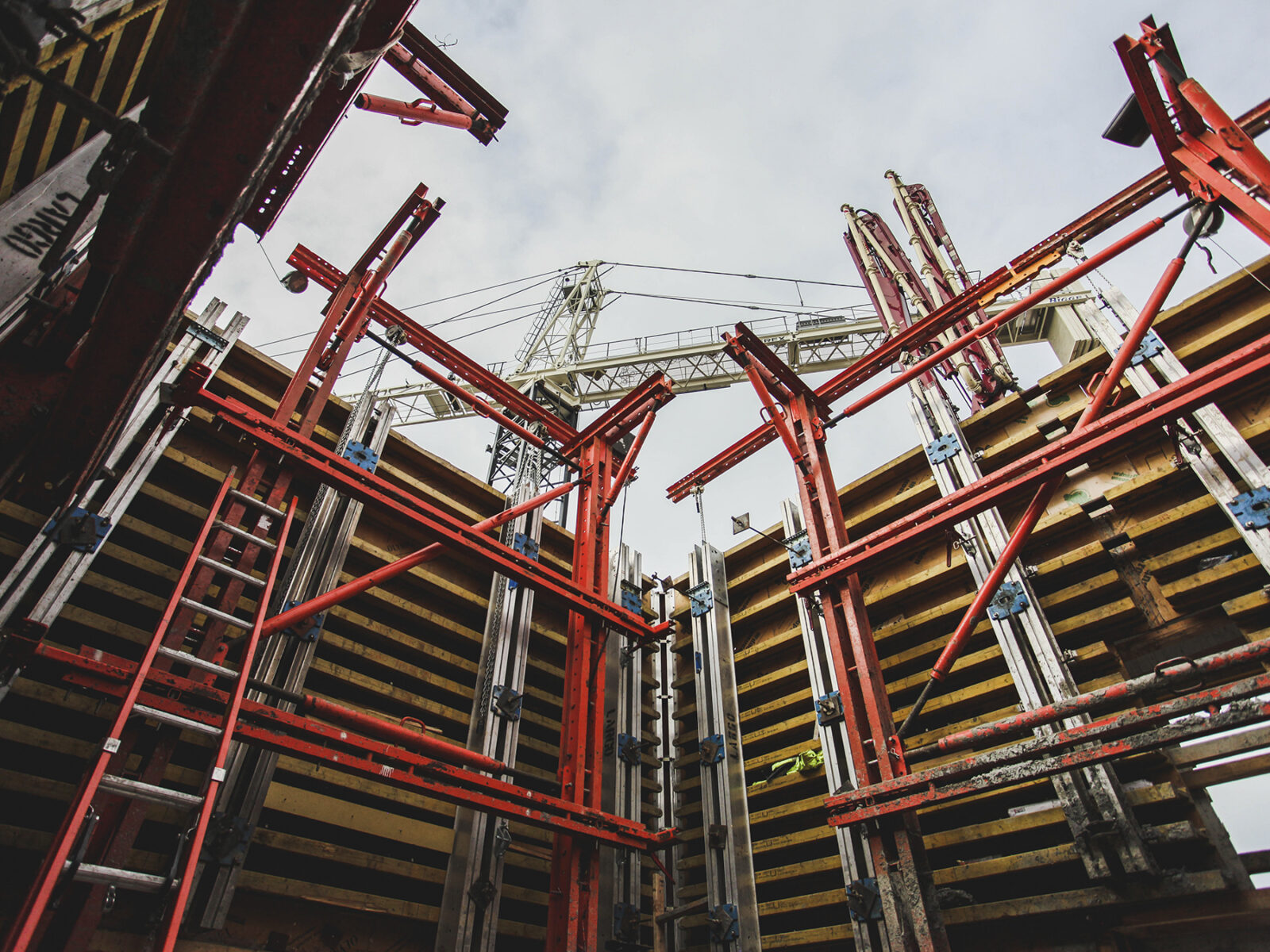
Structural solution: gravity system
Eight-inch thick, post-tensioned concrete slabs span 24 to 30 feet and extend continuously through both the residential and parking programs. Use of post-tensioning within slabs allowed for increased span-to-depth ratios and a flat soffit, free of dropped beams, girders, or column capitals that would interfere with architectural programming and require additional time during construction. By using a regular floor layout throughout, the project’s construction duration and cost were greatly reduced—typical slab construction was achieved in only 5 days for each floor.
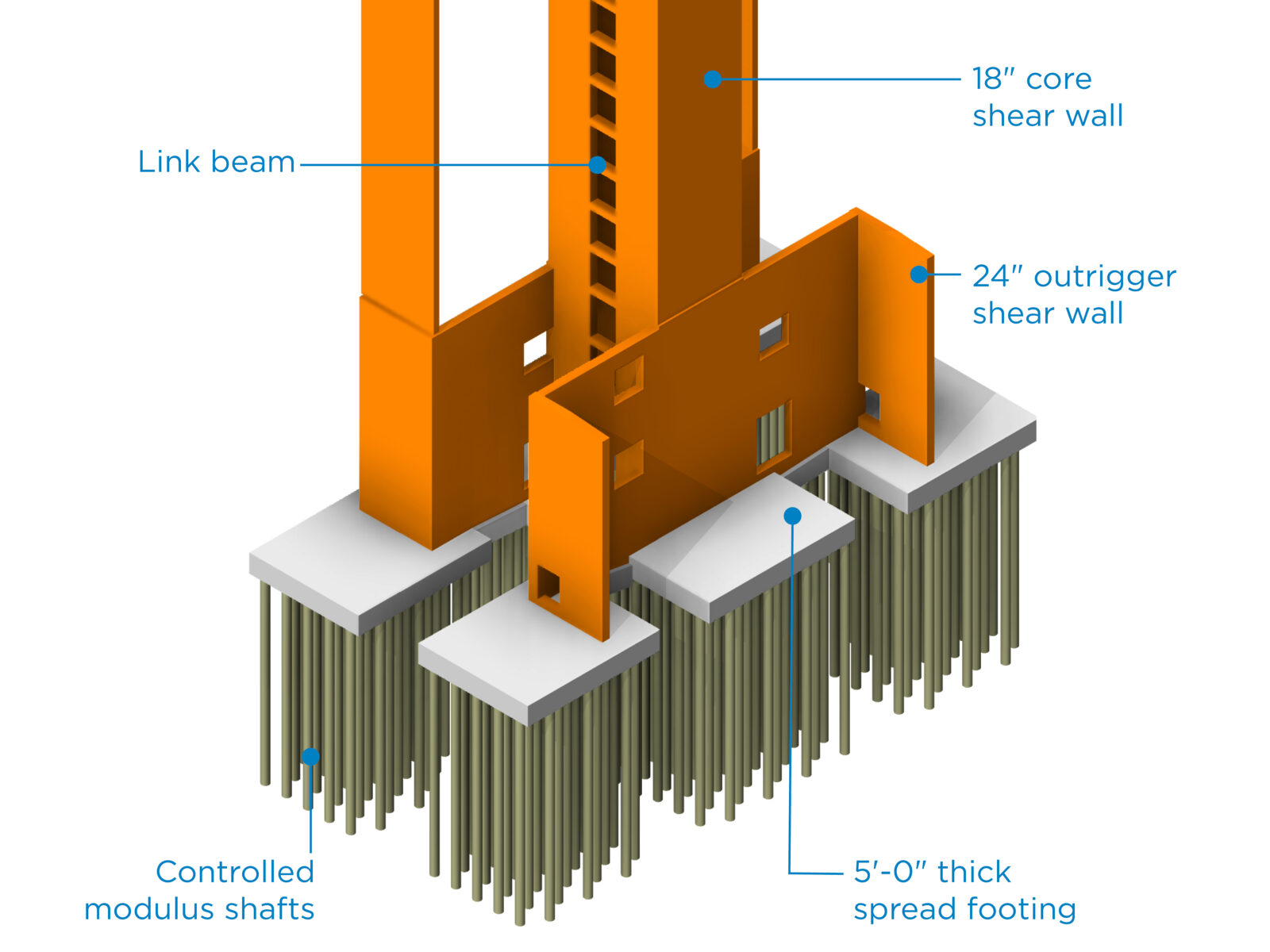
Structural solution: foundation
Controlled-modulus shaft (CMS) piles were used in place of traditional auger-drilled piles at the structure’s foundation. Site permitting, CMS piles provide a means of soil improvement by increasing the effective soil bearing capacity and minimizing the long-term settlements associated with the predominately clay soils. CMS pile construction consists of a drilled shaft that is filled with lean, inexpensive concrete with no reinforcement required. Once cured, the CMS pile increases the density of nearby strata and allows the structure to be supported by less costly isolated spread footings bearing on the uppermost soil layer.
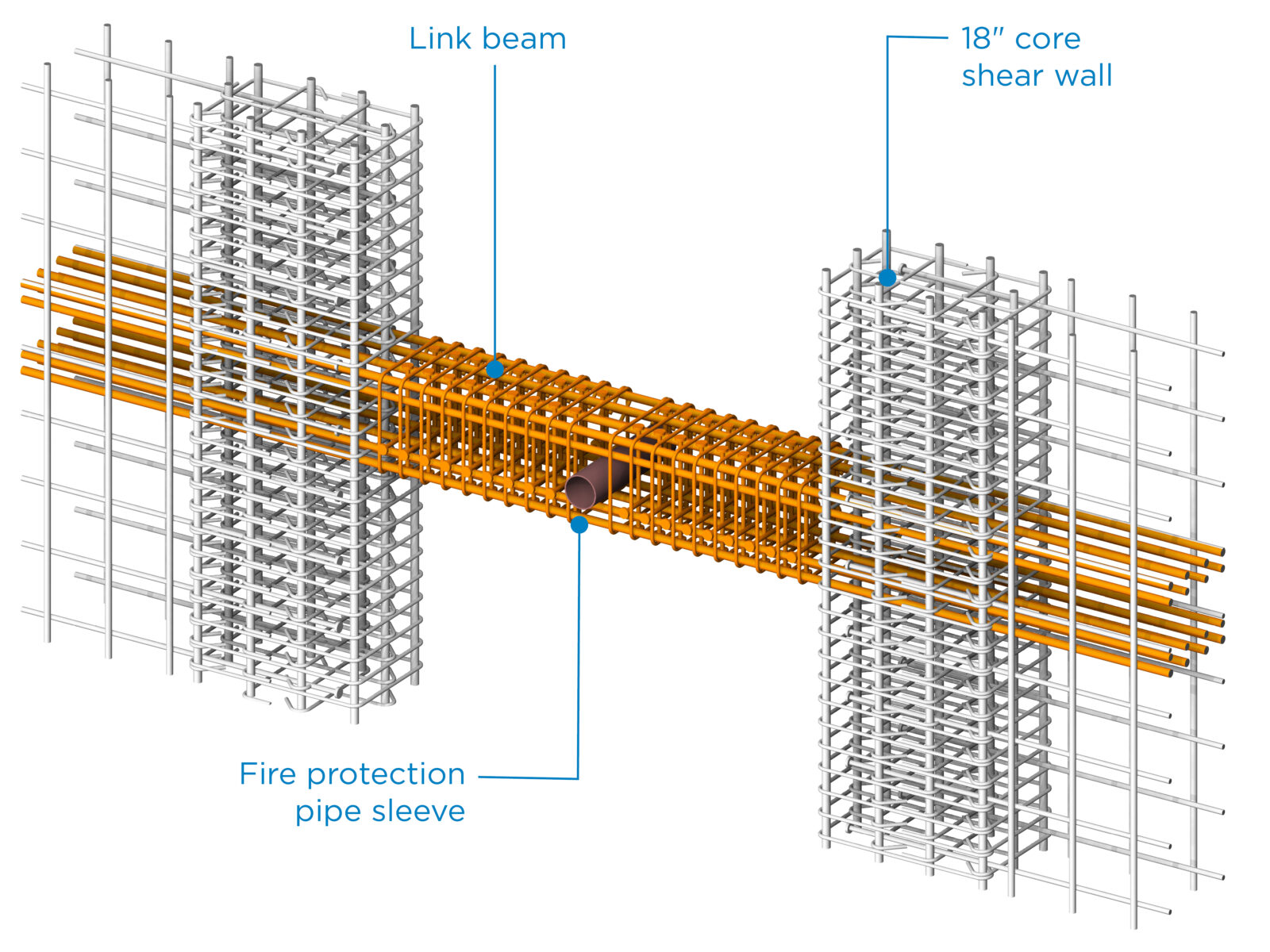
Structural solution: lateral system
The lateral system consists of a network of ductile concrete shear walls and link beams arranged primarily around the elevator core. As the structure’s floor plate grows below the podium level, the footprint of the concrete walls increases, strategically linking them together and engaging with the gravity frame. When resisting lateral loads imposed on the structure by high winds or ground accelerations during a seismic event, the lateral system gathers a portion of the podium’s self-weight through “outrigger” shear walls to stabilize the more slender lateral system within the tower. The design of the link beams that tie the core walls together was critical to both construction productivity and the structure’s seismic resiliency. In order to achieve economy and simplicity, embedded steel sections were avoided and the beams were kept shallow and lightly reinforced. This makes the link beams relatively flexible and not overly strong, which renders them less prone to seismic damage that would degrade performance and create potential hazards due to falling concrete. It also simplified the construction process, eliminating the need to stage additional trades at each slab, resulting in a reduction in construction time at each floor and a significant cost savings when compared to more conventional strategies.